RE_COOLBOX®
PROJECTED WITH STYLE
MADE OF STYROPOR CCYCLED
A CONCRETE COMMITMENT TO SUSTAINABILITY
We are dedicated to ongoing research to provide the market with sustainable products.
That’s why we produce our entire line of RE_Coolboxes ® using Styropor ® Ccycled ® from BASF.
Styropor ® Ccycled® is obtained from chemical recycling of mixed plastic waste and has a reduced
product carbon footprint (PCF*) compared to conventional Styropor ®.
By utilizing Styropor ® Ccycled ®, we are able to adopt a more environmentally friendly approach.
In fact, Styropor ® Ccycled ® has a PCF reduced by about 90% compared to conventional Styropor ®,
while maintaining the same product quality and performance.
*PCF results (emissions and removals) according to TfS: Upstream System Expansion (USE)
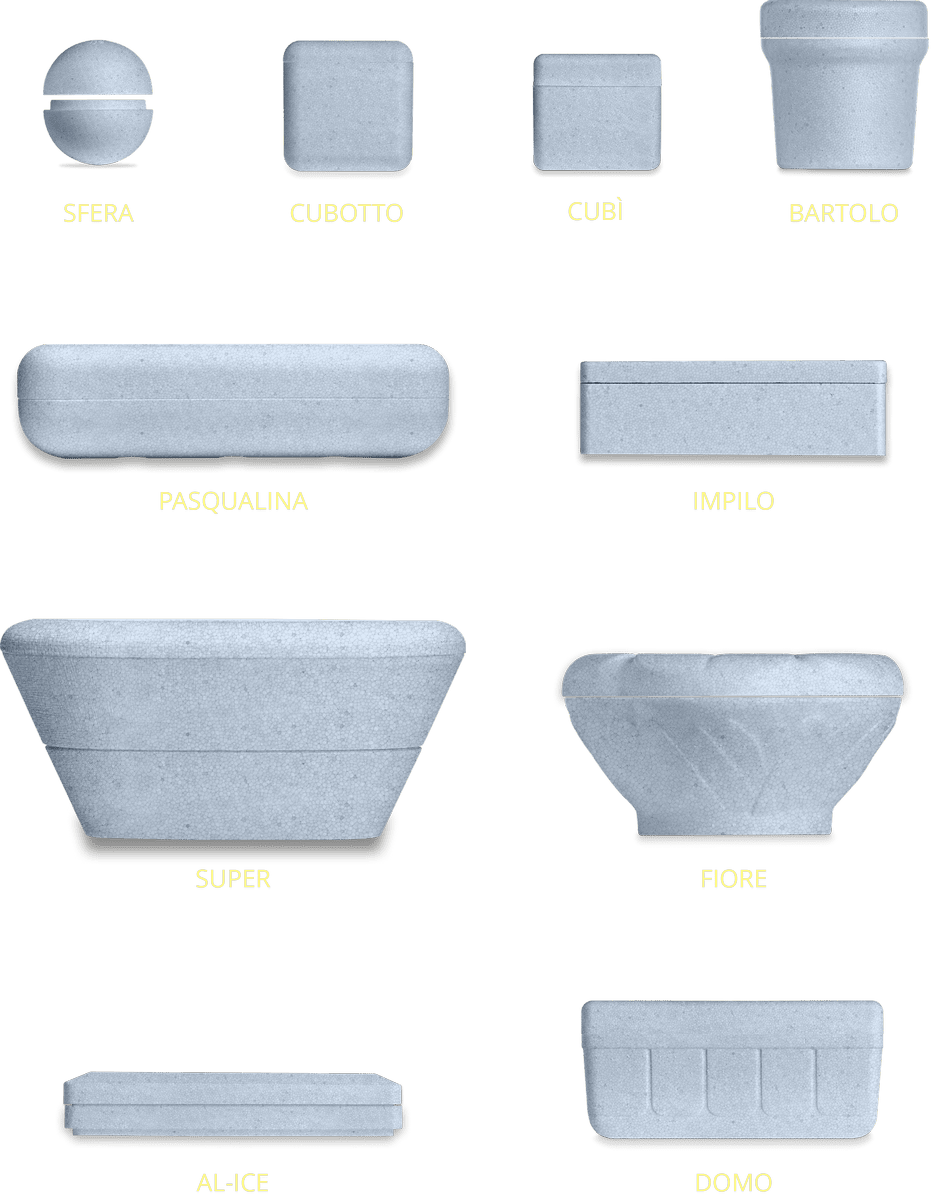

STYROPOR®
C-CYCLED®
Advantages of circularity
In the production of Styropor ® Ccycled ® EPS, fossil raw materials are replaced by pyrolysis oil at the very beginning of the petrochemical value chain using the Mass Balance approach**. This pyrolysis oil is obtained from the chemical recycling of plastic waste that would otherwise be used for energy recovery or go to landfill.
This contributes to a circular economy by turning plastic waste into feedstock for the chemical industry, when no other recycling processes are applicable.
This process enables Styropor ® Ccycled ® to maintain the same technical performance for thermal sealing as conventional Styropor ®, while also meeting the necessary requirements for food contact-an essential feature for our thermoplastics.
**Conventional fossil raw materials required to manufacture BASF products are replaced with recycled feedstock from the chemical recycling of plastic waste or end of life tires along BASF’s integrated production chain. The corresponding share of recycled feedstock, e.g. pyrolysis oil,
is attributed to the specific Ccycled® product via a certified mass balance approach. BASF sites and Ccycled® products are third party certified according to internationally recognized certification schemes like REDcert2 and ISCC PLUS and meet the definitions by ISO 22095:2020. The recycled feedstock is not measurable in the BASF mass balance product. The cradle to gate PCF is calculated according to TfS Methodology using an Upstream System Expansion (USE) approach. USE accounts for a credit for the displaced waste treatment from the first life cycle (e.g. incineration), thereby reducing the product carbon footprint compared to the equivalent conventional fossil product. PCF data is subject to periodical reviews.
Reduced carbon footprint
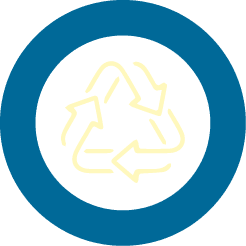
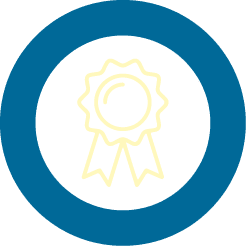
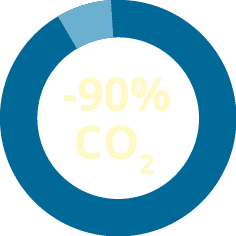
Styropor® Ccycled® has a product carbon footprint (PCF*) reduced by about 90% reduction in
carbon footprint compared to conventional Styropor® produced on the basis of fossil feedstock.
Fossil resources are saved and CO2 emissions are reduced. The significant decrease in CO2 emissions results from chemically recycling the mixed plastic waste instead of incinerating it.
*PCF results (emissions and removals) according to Tfs: Upstream System Expansion (USE)
STYROPOR®
C-CYCLED®
Conservation of resources to protect the environment

1. Consumers dispose of plastic products
2. The plastic waste is sorted and sent to BASF's technology partners
3. The plastic waste is chemically recycled and converted into pyrolysis oil
4. The pyrolysis oil serves as feedstock at the beginning of BASF's production chain.
5. The pyrolysis oil is attributed to Styropor® Ccycled® under a Mass Balance approach
6. New products are produced using Styropor® Ccycled®.
